
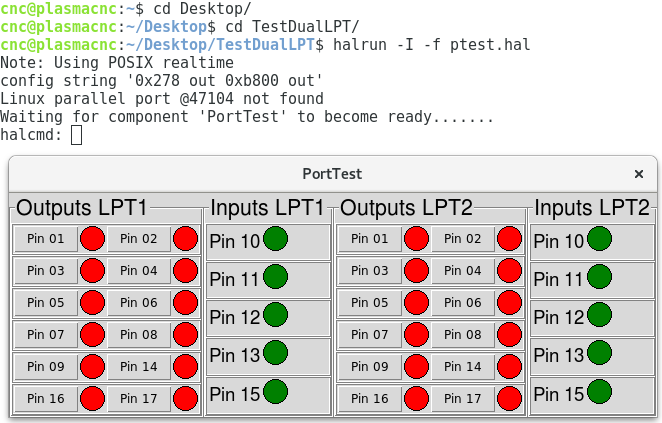
- #PARALLEL PORT CNC MACHINE HESIUSTATES WINDOWS 10#
- #PARALLEL PORT CNC MACHINE HESIUSTATES PORTABLE#
- #PARALLEL PORT CNC MACHINE HESIUSTATES SOFTWARE#
#PARALLEL PORT CNC MACHINE HESIUSTATES WINDOWS 10#
That is part of Windows 10 trying to conserve power.
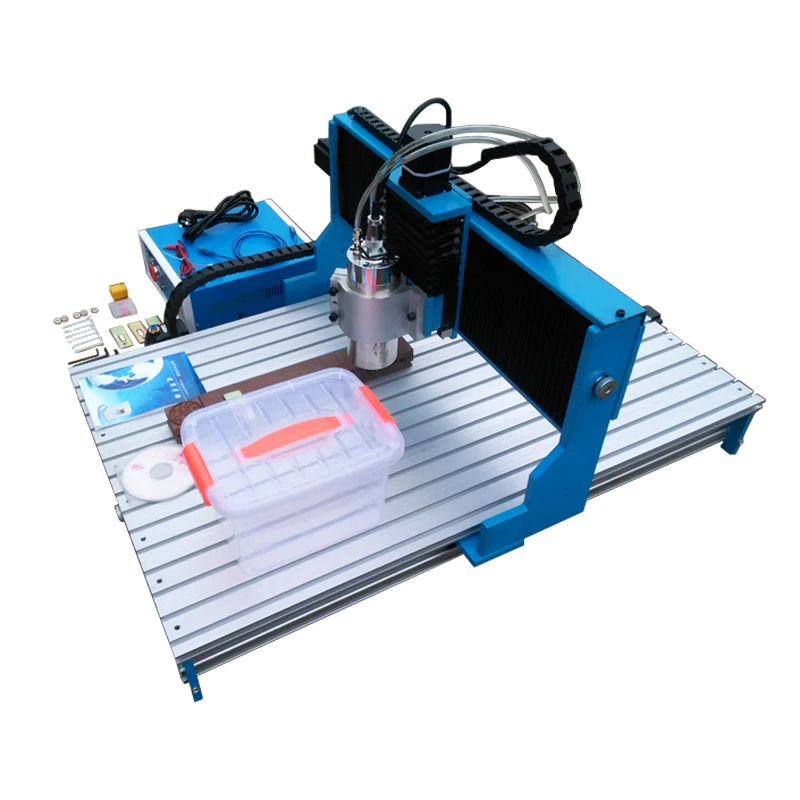
#PARALLEL PORT CNC MACHINE HESIUSTATES PORTABLE#
Photo showing TX14175 PCB track suppling 10V DC to input opto-isolators CNC machining is commonplace in modern industrial manufacturing as the use of NC machining has spread, the ability to program and control portable machine tools has increased. Using the information from the above diagram this should be printerport connections The third buffer output goes to the second of the pins on the 2 pin connector The second buffer output drives the Z, A and B enable connectors Mach3 Minimum Recommended Requirements: Requirements if using the parallel port for machine control: Desktop PC (Laptops are not supported) with at least one. The output of one buffer drives the X and Y enable connectors Mach 3 turns your appropriate PC into a CNC controller, accepting g-code created in your CAD/CAM software, and sending signals to your control box to control your machine. Which is connected to 3 of the 74HC245 buffers That produces the analogue DC control for your spindle motors control board The output of the second buffer drives the opto-isolator at the input of the PWM to analoge converter This product was added to our catalog on May 22, 2010. One buffer output goes to one pin of a 2 pin connector ( next to the B axis 4 pin connector ) They are a fully populated 25-pin cable and the 10 foot length gives the flexibility to locate your PC wherever you want relative to your motor control box. Pin 1 is connected to 2 buffers that are part of a 74HC245 IC ( the 74HC245 is an octal buffer)
#PARALLEL PORT CNC MACHINE HESIUSTATES SOFTWARE#
Mach 3 or what ever control software you use must send the PWM signal to Pin 1 In answer to another thread I traced part of the circuit of the TX14175 BOB In motor outputs under spindle, what should step pin# be set as? as well as Dir pin#. Pin 25: Gnd or NCHello, I was wondering if the pin out would be universal for most of the controllers? I was the prt-e750 and connot get the spindle to move through mach3. Pin 17: PWM 0-10V for VFD Spindle AN1 (if jumper 4 is in default 1-2 position) active low Pin 16: Is supposed to turn Relay 2 on/off but is currently not connected in board. Pin 14: Buffer Chips “Enable” controlled by computer if Jumper 3 is set to 1-2 position Pin 13: Z Axis Limit Switch (active high) Pin 12: Y Axis Limit Switch (active high) Pin 11: X Axis Limit Switch (active high) = when NC switch(es) open Pin 1: Spindle on/off Relay 1(active low) If it is JP-3163B ver 3.9, here are the pinouts Open the box and check the model of the control box.
